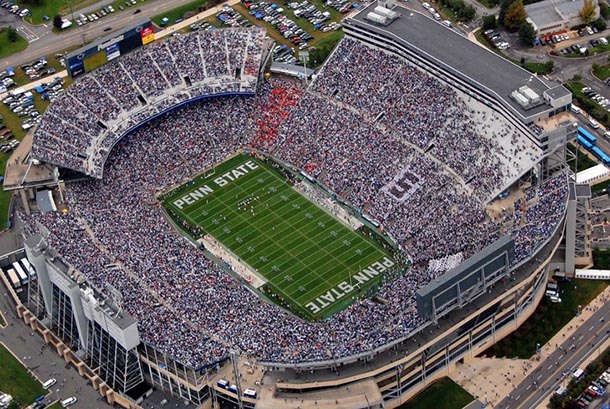
Beaver Stadium as seen from a helicopter during a Penn State-Syracuse game in 2009. IMAGE: TINA HAY
Improving the fan experience at Beaver Stadium
Student projects work to reduce wait time at concession stands and restrooms
3/28/2019
By Shane Ramsay
UNIVERSITY PARK, Pa. — Fans could soon see shorter lines at Penn State home football games, thanks to some innovative thinking from Penn State engineering students.
Penn State’s Service Enterprise Engineering initiative (SEE 360) and Beaver Stadium have worked together for more than a year, leading to two capstone projects that occurred this past fall semester. One project, sponsored by Penn State Athletics, focused on optimizing the efficiency of the concession stands and the other project, sponsored by SEE 360, focused on finding solutions for women’s restroom lines.
Charlie Purdum, assistant teaching professor and director of industry relations in the Harold and Inge Marcus Department of Industrial and Manufacturing Engineering at Penn State, and faculty adviser for both groups, explained the importance of these projects, saying that football fans deal with a lot of “conflict” during their game day experience, such as parking, bathrooms and lines. He said improving these customer service issues are vital to keeping fans coming to the games, instead of opting to watch them at home on television.
Reducing concession stand wait time
Students Lisha Li, Andrew Phoebe, Saulabhya Shrikant, Yijin Wang and Jinyu Zhao designed their project to improve customer service through decreasing wait times for the concession stands. This centered around the production and service of chicken baskets, which serve as the most popular and profitable item on the menu.
Former SEE 360 collaborator and research coordinator Anthony Petrine, who was involved in the planning and data collection portions of the project, described how the group’s main objective in its research was improving everyone”s game-day experience.
“We wanted to reduce the wait times in the lines, because what ends up happening is you have lower customer service with the longer waits,” said Petrine. “People are buying tickets to watch the game, not stand in a line.”
The group collected data at the September and October games against Kent State and Michigan State, respectively. This included timing the interactions between customer and stand attendants, recording stockout frequencies, and documenting the time needed for the cooking and production of chicken baskets. They also spoke with the stand attendants, who are volunteers from Centre County organizations, about inefficiencies from their perspective.
After their final analysis and the completion of a simulation model, the group recommended the implementation of an “express chicken basket,” where students would use vouchers or tickets that they purchased the week before the game, presenting those upon their arrival to the stand. They found that this would decrease the average customer wait time by 52 percent from around 19 minutes to approximately eight minutes. It also would increase the number of customers served by almost 10 percent.
SEE Fellow and doctoral student Kai-Wen Tien, who also was heavily involved in the project, explained how the knowledge gained by these students in the classroom can be used in a wide variety of ways.
“The method that we used is a very classic method for manufacturing, but we applied it to the service industry,” said Tien. “It serves as an example for how we can use manufacturing methods to change other industries.”
Reducing wait time for restrooms
The second capstone group, sponsored by SEE 360, was composed of students Matthew Bessasparis, Brady Bobbit, Matthew Chabala, Hamza Fadil, Bowei Han and Zichao Zhang. Their research sought to tackle a problem that occurs at many large, entertainment venues: disproportionately longer lines for the women’s restrooms as opposed to the men’s restrooms.
“Our goal was to observe the women”s restrooms in Beaver Stadium and try to alleviate the wait times, as well as improve customer satisfaction,” said Chabala, a computer science senior. “So, if there is a line, we want to make it as pleasurable as possible for the fans.”
Data collection also occurred during the games this past fall against Kent State and Michigan State and involved observing and recording restroom wait times.
“We recorded the times of when they [fans] got in the line, when they got to the front of the line, and when they got out of line, as well as how long it took them to use the stalls and sinks,” Chabala said. “And from there, we made models on computers to simulate real life. Once we had those models, we would modify them to see how the efficiency could increase or decrease.”
Following the analysis of their simulation model, the group proposed three solutions that would decrease the restroom wait time by about 15 percent. These consisted of signs being placed throughout the stadium to direct guests to under-utilized restrooms, removing a portion of a large wall in each restroom that blocks the view of half of the stalls, and creating a line barrier to improve the flow of the concourse and alleviate line-cutting.
“This project made me realize that service engineering encompasses a large part of our day-to-day life,” Bobbit, an industrial engineering senior, said. “It’s really cool how you can study these real-life scenarios and look at the customer in terms of their expectations and perceptions of the service and how we can optimize that for a better customer experience.”
Cory Chapman, associate athletic director for facility and event operations, believes the athletic department’s collaborations with students in the Learning Factory has been “fantastic” and is excited to implement improvements based off their research.
“It’s been a great partnership,” said Chapman. “We continually look for ways to improve the fan experience at all of our venues. There’s already a lot of positive things happening, but these students have looked into ways that we can tweak or enhance the experience for our fans.”
Purdum noted how projects like these not only apply to Beaver Stadium but can be universally applied to improve any venue that provides these types of services.
“Any public venue could benefit from these projects, whether it’s a stadium, an arena or a theater,” said Purdum. “Any place where you have an event that people are coming to see, and they’re buying refreshments or food and they’re going to the bathroom, could use this knowledge.”
The collaborations with Beaver Stadium continue to be a mutually beneficial experience. The efficiency of the women’s bathrooms remains an ongoing project for engineering students, and in the coming semesters, students will begin to research ways to make the entrance lines at each gate more efficient.
“These examples illustrate the opportunity for engineering to contribute to the service sector,” said SEE 360 Advisory Board Chairman Chuck Schneider. “Poorly engineered service processes are everywhere around us, waiting for engineers to improve our lives, improve service organization performance, and build rewarding careers while doing so.”
Kudos came from other sectors of the University as well. Law Professor Stephen Ross, who directs the multidisciplinary Penn State Center for the Study of Sports in Society, praised leaders in the College of Engineering and Intercollegiate Athletics for their collaboration.
“We are harnessing students’ passion for sports to help them gain critical skills,” Ross said. “The students displayed not only technological expertise but learned how to solve real-life problems and present their findings to an audience who lack their engineering know-how. The benefit is not just to the students but to Nittany Nation.”
With more than 80 percent of the U.S. economy based in the service sector, the mission of SEE 360 is to contribute to engineering the 21st century. This includes developing teaching resources such as textbooks and case studies that apply engineering techniques toward solving problems in service industries. To learn more about SEE 360, visit see360.psu.edu.