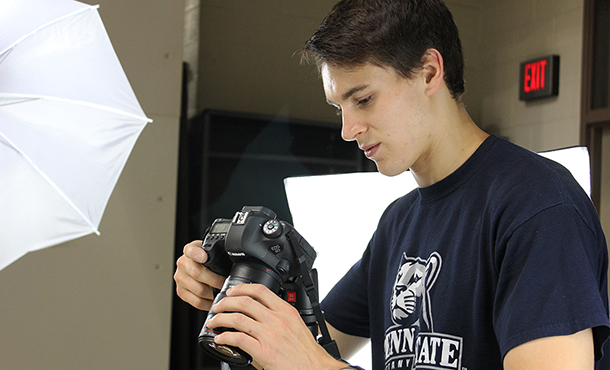
Andrew Bellows, an mechanical engineering undergraduate student, takes photos of a bottle opener from different angles in order to generate a point cloud from which the object can be 3D-printed.
Digital photography: The future of small-scale manufacturing?
9/19/2016
UNIVERSITY PARK, Pa. — What if it were possible to quickly and inexpensively manufacture a part by simply using a series of close-range digital images taken of the object?
Michael Immel, instructor in the Harold and Inge Marcus Department of Industrial and Manufacturing Engineering, originally started thinking about the technique, called photogrammetry, for a different purpose, but quickly realized its application in manufacturing.
“If we can take pictures of the parts and use commercial software to create the point cloud file from the images, we can come up with the dimensions within some reasonable amount of accuracy and apply it in industry,” Immel explained.
In this technique, digital images of an object that have been taken at various angles are used to create a point cloud – or a large collection of points used to create 3D representation of existing structures – from which a computer-aided design (CAD) file can be generated.
The resulting CAD file and subsequent 3D model could then be presented used to rebuild the part, or 3D print it, to its original specifications without using traditional methods, which are both expensive and time-consuming.
Immel received a seed grant from the Marcus department’s Entrepreneurship and Innovation Fund to explore if photogrammetry can be a more efficient way of manufacturing low-tolerance parts – or parts that have sufficient limits of variation and do not have to fit into assemblies – such as large pipes and manhole covers, rather than using traditional methods.
Over the summer, Immel and three engineering students – Andrew Bellows, an undergraduate student in mechanical engineering; Benjamin Sattler, an undergraduate mechanical engineering student and a Schreyer’s Scholar; and Xinyi Xiao, an industrial engineering graduate student – set out to test the accuracy of photogrammetry.
The group chose parts for which they already had a CAD file to compare with their photogrammetry-created point cloud files.
To get started, Bellows created a specific studio setup to take consistent and replicable photographs of the part. The environment included even lighting, to eliminate shadows, and a contrasting background to ensure the photo obtained enough data from the part. Additionally, Bellows took overlapping photos around the part at a specific angle and from different distances to be sure he had enough images to create the point clouds.
Bellows, Sattler and Xiao then each used a version of software used for photogrammetry – Photomodeler Scanner, AutoDesk ReMake and Mathworks MatLab – to create point cloud files, which were then compared to each other and to the original CAD and point cloud files.
“We looked at the variance between the original point cloud files and photogrammetry point clouds to see if there are discrepancies between them and to determine how accurate this technique would be if it were to be used in manufacturing,” said Immel. “Photogrammetry has proven to be an accurate approach for applications where tight tolerances are not necessary.”
In a traditional manufacturing process, large quantities of parts are made in quick succession and then go from the manufacturing line through an inspection process. A quality control engineer or specialist then measures the parts with handheld tools and check for any abnormalities, making sure all of the dimensions of the part are within tolerance so they operate as the part was originally designed.
“The ideal application of photogrammetry in the industry setting would be to have a vision system in a manufacturing plant that included cameras fixed on the machines making the parts, taking continuous photos,” explained Immel. “Live data could be sent back to an engineer or a quality control employee and they could compare the point cloud that has been derived from the digital images to the point cloud of the original file and determine if the part is within tolerance or not.”
Immel and his team have concluded that photogrammetry has the potential to make the quality control process quicker, less expensive and more efficient for manufacturers.
Saurabh Basu, an assistant professor in the Marcus department, recently joined Immel’s research group and is interested in looking at photogrammetry from an empirical research standpoint.
“Now that we have a process in place that works, we need to hone it. Dr. Basu will help us by providing us with the empirical data before we take the process to industry to test it out,” said Immel.
The research the team has done so far is only the beginning. Immel as his students are continuing the research this fall and are working on a proposal in the hopes to secure additional funding from the National Science Foundation.